Metal 3D printing as game changer for mass production of EURO7 compliant brake discs
With EURO7 introduction particulate matter emissions from brakes are regulated for the first time. Widely chosen technology to meet these new requirements is laser coating of brake discs with wear-resistant layer. Learn more about HS-LMD in this talk held by TRUMPF.
With EURO7 introduction particulate matter emissions from brakes are regulated for the first time. Widely chosen technology to meet these new requirements is laser coating of brake discs with wear-resistant layer, also known as High-Speed Laser Metal Deposition (HS-LMD). Metal powder with hard material supplement is sprayed onto the disc friction surface using high-power lasers.
The coating process and coated brake discs must meet more requirements than emission limits. For economical series production, a high degree of powder utilization and process reliability for constant coating quality are essential. Brake discs must comply with high industry standards, ensured through intensive stress testing. Manufacturability must be guaranteed for complex brake disc geometries.
Besides optimal laser beam adjustment with beam forming, fulfilling these requirements is enabled by characteristics of the superimposed powder flow, essentially formed by the powder nozzle.
Significant optimizations are presented, directly achieved or indirectly enabled by changing the TRUMPF nozzle from classic production to 3D printing using laser powder bed fusion. Inner contour and cooling structure have been optimized for high thermal loads in continuous use. Geometric degrees of freedom in the nozzle shape allow using the TRUMPF bifocal laser technology and individual adaption of nozzles to brake disc contours.
Presentation language: GER
(English translation will be provided on site)
Speakers (1)
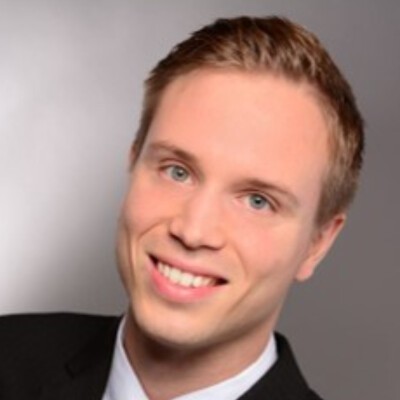