Influence of arc oscillation frequencies on the surface of DED-Arc manufactured Ti-6Al-4V structures
- Oscillation frequency in WAAM has a major influence on the resulting surface properties - By using high oscillation frequencies, the specific energy consumption can be reduced through better material utilization - Energy consumption of the robot is negligible
Directed energy deposition based on gas metal arc welding (DED-Arc) is increasingly used for large or coarse near-net-shape structures. Also known as wire arc additive manufacturing (WAAM), DED-Arc produces additive structures, which have a large surface roughness or waviness compared to other additive processes. This results in a large machining allowance, especially at high build rates. In order to improve this surface quality, this study investigated the relation between the oscillation frequency of this arc process on the resulting surface of a Ti-6Al-4V structure. Therefore, multi-layer single pass tracks which perform a sinus like path are used. The surface improvement was then compared to the additional energy required by the robot due to increased oscillation speed and evaluated using the specific energy consumption (SEC). In a first step, several walls were manufactured at maximum wire feed of the system. Here, only the oscillation frequency (OF) was varied in order to obtain the same energy per unit length for all test structures and to ensure comparability. By increasing the OF from 1 to 4.5Hz, a significant improvement in the surface was initially achieved and a proportional relationship was observed. This is also linked to an improvement in the buy-to-fly-ratio (BTF) and ultimately the carbon footprint, since less volume has to be machined due to lower surface waviness. By increasing the OF and thus increasing the welding torch speed and acceleration, a higher energy requirement from the robot system was determined in a second step. In a comparison, it was then shown that the additional robot energy leads to a reduced machining allowance thanks to the resulting better surface. But in total, this results in a lower SEC for a demonstrator structure, since the additional robot energy is a magnitude lower, than the energy input of material savings.
Vortragssprache: ENG
Sprechende (1)
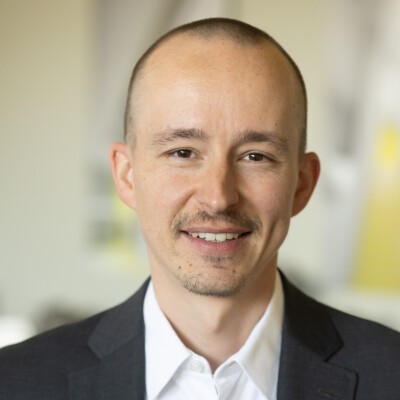