Temperature control by simulated adaptive layer times in powder bed fusion processes
With the ever-increasing energy input in modern PBF-LB/M systems, the issue of temperature monitoring and control is becoming increasingly important.
In this work, a simulation-based thermal management model for metal parts produced through powder bed fusion (PBF) is proposed. PBF is an additive manufacturing technique that employs a high-energy beam to selectively melt and fuse powder particles layer by layer. The productivity and efficiency of PBF processes can be significantly increased by using multi-laser systems with larger build volumes. However, this approach affects the parts' thermal history, which can significantly impact their mechanical properties, microstructure, and defects.
To address this issue, an algorithm has been developed to calculate adaptive cooling times reaching predefined temperatures at the end of each layer. The algorithm is used in a fast thermal process simulation using layer lumping. The simulation model is applied to a modern multi-laser machine, and the effectiveness of the adaptive cooling times and minimal layer times is evaluated. The results indicate that lower maximum temperatures can be achieved in less manufacturing time with adaptive cooling times than with minimal layer times. However, the significant increase in manufacturing time highlights the need for active cooling systems to utilize multi-laser machines fully.
In summary, this paper presents a significant contribution to the field of additive manufacturing, emphasizing the importance of thermal management in ensuring the quality and performance of metal parts produced through PBF.
Vortragssprache: ENG
Sprechende (1)
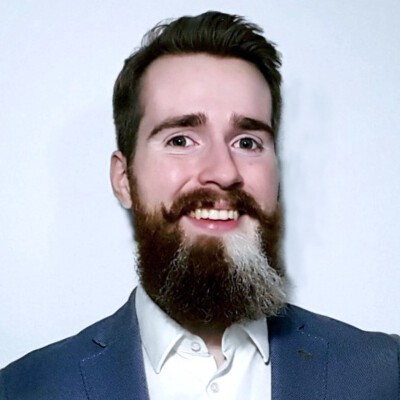